RDF Processing Plant Solutions
Our RDF processing plant solutions are designed to convert solid waste into Refuse Derived Fuel (RDF) pellets, a sustainable and high-energy fuel source. Our advanced waste management processes ensure efficient, environmentally friendly, and cost-effective conversion of waste materials, making us a leader in the waste-to-energy industry.
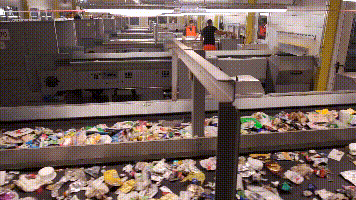
Manual Sorting Solutions
For countries with low labor costs, a combination of mechanical and manual sorting can be used, which is a cost-effective waste sorting and recycling solution.
Read More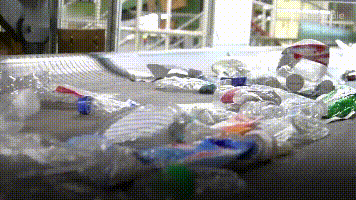
AI Robot Sorting Solutions
The artificial intelligence sorting robot with autonomous learning can practice and accumulate sorting data. It can effectively sort various high-value recyclables.
Read More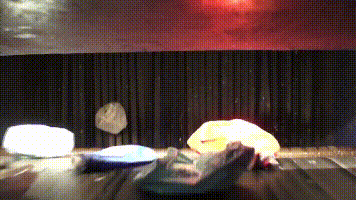
Optical Sorting Solutions
Optical sorter is a automatic sorting device based on sensors, high-speed ejector valve has large processing capacity. It is a good choice for bulk handling project of waste recycling.
Read More